The ingenious design of the aluminum beverage can is often overlooked, despite the fact that nearly half a trillion of these cans are manufactured every year - that's about 15,000 per second. Engineers have carefully considered the shape of the can, opting for a cylinder rather than a sphere or a cuboid. A cylinder offers the smallest surface area for a given volume, using the least amount of material and providing no weak points due to the uniform stress on the walls. However, a sphere is not practical for manufacturing and a cuboid is uncomfortable to hold and drink from. Therefore, a cylinder is the optimal choice, combining elements of both shapes. To create a can, engineers start with a disc called a blank punch, made from an aluminum sheet about three tenths of a millimeter thick. The process begins with a drawing die and a blank holder that rests on top. A cylindrical punch presses down on the die, transforming the blank into a cup. This cup is then redrawn to a narrower diameter, making it taller. The redrawn cup is now the final diameter of the can. To increase the height of the can, a punch pushes it through an ironing ring, resulting in thinner walls. The bottom of the can is then formed into a dome using a convex doming tool and a punch with a concave indentation. The dome reduces the amount of metal needed to manufacture the can. Engraved numbers on the dome signify the production line and body maker number, helping troubleshoot production problems. In the factory, the manufacturing process occurs at a rapid pace. Redrawing, ironing, and doming all happen in one continuous stroke in just 1/7 of a second. The punch moves at a maximum velocity of 11 meters per second and experiences a maximum...
Award-winning PDF software
Video instructions and help with filling out and completing Can Form 2220 Historical
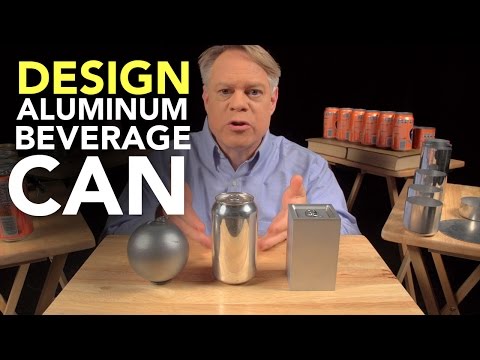