Music welcomes you to the exodus lecture. This is Module 4, Lecture 1. In this lecture, we will be studying various geometrical measurements of both pieces. Specifically, we will discuss the importance of geometric integrity of our pieces, definitions related to geometry measurement, and symbols used to represent geometric tolerancing. Additionally, we will explore the use of a surface plate for inspection purposes. We will also provide a brief description of a surface plate and discuss the meaning of straightness and straightness tolerancing. Furthermore, we will examine different methods for measuring straightness. Understanding the importance of geometric integrity in components is crucial. There is an increasing demand for product reliability and efficiency, which highlights the need for geometric integrity. Components must be produced according to strict specifications set by the designers to ensure expected functionality. However, deviations from the nominal features often exist in the components. These deviations must be controlled during manufacturing. Irregularities in workpieces can be broadly categorized into micro irregularities and macro irregularities. Micro irregularities include roughness, waviness, and surface contamination, while macro irregularities involve errors in size and form. Deviations from the ideal form, known as form errors or geometrical deviations, have a significant impact on component ance. For example, errors in cylindricity in hydraulic systems can affect the efficiency of products such as hydraulic pistons, motors, and pumps, leading to increased friction and leakage. It is essential to control manufacturing errors and measure deviations to ensure components are within the prescribed tolerance limits. In engineering applications, measuring geometrical features poses challenges, including straightness, squareness, flatness, roundness, cylindricity, parallelism, concentricity, and run-out. In this lecture, we will focus on the methods used to measure straightness. Additionally, we will discuss various definitions related to geometric deviations in components. In many cases, we use the term "feature" to describe...
Award-winning PDF software
Video instructions and help with filling out and completing What Form 2220 Determining
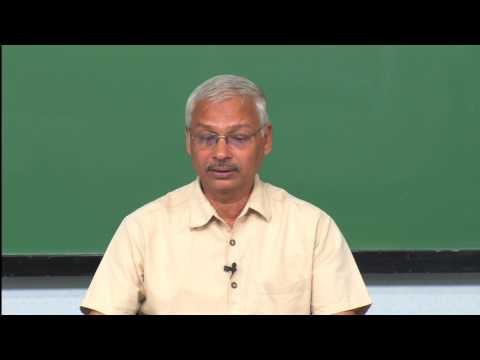