Hi, I'm Ben and this is the house I built out of shipping containers. I've been interested in shipping container architecture for quite some time, but I had a really hard time finding good information about how to get building permits or how much it would cost. Well, we did the research, documented everything that we did, and now we're so excited to share with you what we learned. So, check it out! This is episode 1 where we'll talk about buying containers, getting building permits, and pouring a concrete foundation. In the spring of 2018, I bought 10 acres of land in Joshua Tree, California. It's a square piece of land about 650 by 650 feet, and it has this nice little mountain right in the middle. While I was waiting for the surveyor to finish up the site drawings, I went ahead and ordered two shipping containers. Now, I had heard, like a lot of people, that you can get shipping containers for really cheap. But in California, you have to use a one-trip conditioned container if you're turning it into a permitted house. This is just so that you can provide documentation for what's been inside the container, just to ensure that there hasn't been any radioactive or toxic stuff in there. I also didn't order typical containers. I ordered hi-cubes, which were a foot taller than a standard shipping container. This is gonna give me more room for insulation, running wiring, and of course, because we're in California, sprinkler systems for fire suppression. Originally, I was only planning on using one 40-foot container to build one tiny house. But then, I thought it'd be really nice to have a guest bedroom and bathroom for visitors. And then when I checked in with my local building department, they informed me...
Award-winning PDF software
Video instructions and help with filling out and completing Why Form 2220 Foundations
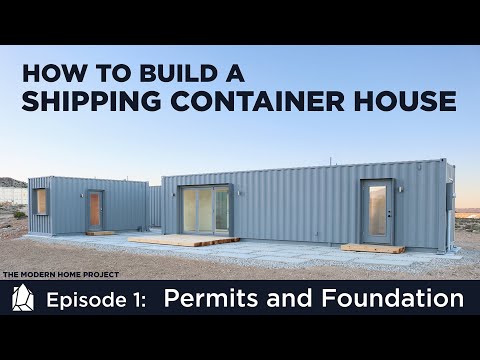